Automotive
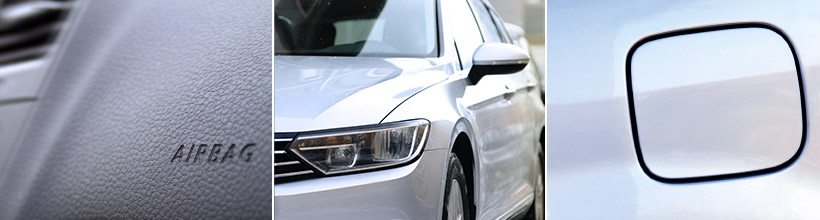
Flawless surfaces that are, amongst others, determined by a uniform surface appearance, are the hallmarks of vehicles. This applies to the bodyshell, as well as to the interior. Even the smallest of deviations that become visible under certain lighting conditions can be considered as undesirable to the customer and impair the overall impression. This is why objective, human-independent evaluation is gaining in importance in numerous stages of the production process.

In recent years, the use of plastics has increased in vehicle design, as is the case with the outer skin. Examples:
- Injection molded components such as car fender, fuel doors or covers on the door or sliding roof
- Composite parts (SMC) such as tailgates or spoilers
The surfaceCONTROL inspection systems recognize and evaluate the shape deviation on these components and help to reduce the quality costs and to avoid waste or rework. These systems are able to recognize relevant deviations from 5 ... 50μm (according to the surface) within a few seconds (1 ... 10s) and to evaluate it objectively. Even the slide marks of the bolt with a height of about 1μm can be recognized. The surfaceCONTROL inspection systems can be used in different stages:
- Development up to the first prototype
- Tool and die manufacturing
- Series production start-up
- Series supervision (sample checks or 100% inspection)
- Inspection of quality of already produced or bought-in components

The overall impression of a vehicle's quality is strongly influenced by its interior. This is why high quality materials, tight manufacturing tolerances and the perfect assembly of interior components are critical. One key aspect is the control panel and dashboard, which can always be seen by the front seat passengers. As well as the visual requirements, functional and security requirements also have to be fulfilled. For this reason, the passenger airbag has a predetermined breaking line which is generated using a laser. This »weak point« ensures the safe opening of the airbag at the predetermined breaking line. Due to the heat input when fixing the airbag in place, or because of the mechanical pressure of the control panel, sink marks may appear, which can be recognized under certain light conditions.An objective visual evaluation of this sink marks is difficult and the grained surface makes tactile measurement impossible. The surfaceCONTROL systems enable fast, objective evaluations to be made of the characteristics of any shape deviations, both on grained and smooth surfaces.

One of the main application fields of surface inspection system is the identification and analysis of deformations and discontinuity in automotive body shell parts. In modern stamping lines, automotive body shell parts are produced in a cycle time of a few seconds. The processes which have to be controlled are very complex and require lots of experience. Because of the different fouling, material tolerances or variations in the process, unwanted shape defects such as pimples, bumps, dents and neckings may appear. A visual recognition of these defects on metallic surfaces is almost impossible. For production release and after defined time intervals (0.5 – 1h) such components are chosen, whose surface is completely checked by physically feeling or pulling with a stone. This process is highly complex and contains the risk of not recognizing failures.With every step in the manufacturing process the value of the components and the effort involved in reconditioning increases. In-process detection and retraction of the failures helps to minimize quality costs. With the surfaceCONTROL product line INB has developed a system that scans the surface of the car body components with a 3D sensor in a few seconds and offers the detection and evaluation of local defects. A digital stone, for example, is used for the analysis. This block is moved over the 3D-data of the surface like a physical block. The length and direction of the block is adjusted according to the shape of the surface. The result is the DefectMap; a graphical representation of the defect with exact information about the height and depth. The determined values can be used for an automatic OK/NOK-decision.All body shell parts made of metal are inspected; beginning with the pressing machine to the assembly line, the body in white to the EPD coating. The sensor can be mounted to a robot for the inspection of body components.